Video Transcript
Why Are Springs Used With Seals
The main reason to use a spring would be to overcome the limitations of the primary seal element.
Generally, seals made from elastomer and most polymers can energize themselves at least for a short time under certain conditions. However, as application parameters broaden, spring energizers are needed to provide consistent loading.
There are four types of springs commonly used in the industry:
- Garter Springs
- Cantilever or V Springs
- Helical-Wound Springs
- Canted-Coil Springs
1. Garter Springs
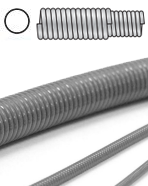
The garter spring is constructed of a thin wire that is coiled and back-wound on itself, which resists stretching or being pulled apart. They are most commonly used on a radial shaft seal and helps the lip engage the shaft. There are many different combinations of wire and coil diameter, which allows us to select predictable loading across a wide range of seal diameters.
They are a good option when we have high runout in our shaft allowing the shaft seal to maintain contact with the shaft and unlike the rest of the seals we’ll talk about today. Garter springs do not require an opposing surface to push against.
2. Cantilever or V Springs
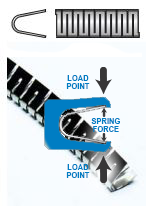
The next type of spring is the cantilever or more commonly known as the V spring. It is made up of a metal strip that is punched and formed into a “V” shape. This spring geometry allows for a wide deflection range in a predictable linear load.
The shape of the spring also concentrates the load at the front of the seal – making it a good choice for excluders or scrapers in reciprocating applications. It can also be a good choice for static applications where we have wide tolerances or misaligned glands.
3. Helical-Wound Springs
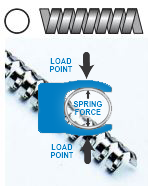
A helical wound spring is constructed of a thin metal strip that is formed into a helix shape. This geometry produces a high load versus deflection curve – making it a good choice for vacuum or cryogenic applications.
These are commonly selected for static applications. But sometimes we can use them in slow or infrequent Dynamic conditions.
The small deflection range of this type of spring prevents us from using them when we have wide intolerances or misalignment.
4. Canted-Coil Springs
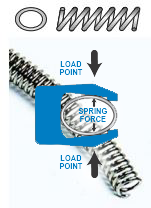
Finally, a canted-coil spring is made from a round wire that is coiled and then formed into a slanted shape.
These types of springs have a very flat load versus deflection curve – making them a great option when we do run into a large gland tolerance or a misaligned condition.
They are also good options when we run into a friction-sensitive application because as the engagement of the lip changes the amount of loading generated by the spring does not change.