Housing Recommendations
Material - The most commonly used materials for seal housings are steel and cast iron. Care must be taken when softer housing materials such as aluminum, bronze or plastic are used.
Housing Finish - A finish range of 40 to 100 μin Ra (1.0 to 2.5 μm Ra) is recommended. The Clipper seal is more tolerant of housing finishes that are toward the upper limit than metal OD seals.
Housing Profile - A lead-in chamfer per the following example is highly recommended for all seal housings. The chamfer aligns the seal during installation and helps prevent the seal from cocking. Both corners of the chamfer should be free of burrs and sharp edges to eliminate OD damage during installation.
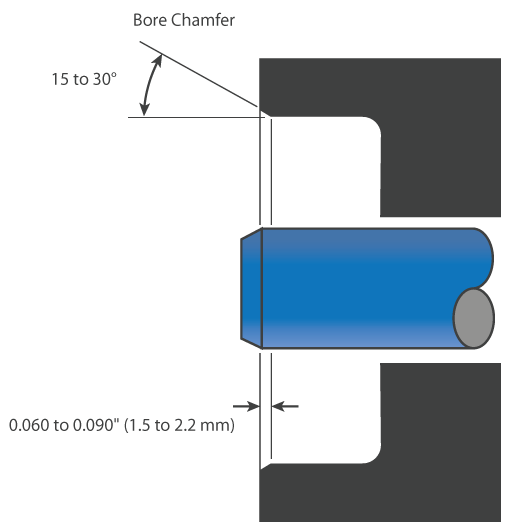
Housing Tolerance - The diametrical tolerance of the housing for Clipper Oil Seals should be within the limits.